Fields of competence
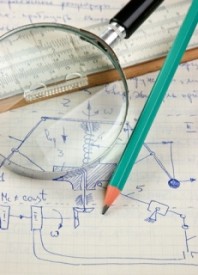
ROBOTNOR represents a unique synergy of academic and industrial expertise which allows us to counsel and comprehend a wide variety of tasks and projects. Our fields of competence are numerous and diverse.
Industrial robots are the relentless workforce of the industries. They pick, place, paint, and weld a wide variety of objects. They are automatically controlled, reprogrammable multipurpose manipulators. The backbone of their actions is the sensors and software driving them. The software represents implementation of advanced algorithms and mathematical models developed to increase accuracy, reliability and efficiency of the manipulators. Knowledge of its environment and modular tool handling gives industrial robots the capability of handling a wide variety of tasks. As the application areas of industrial robots are increasing, the human-machine interface is changing. The robots are usually manipulators with a few degrees of freedom and exchangeable tools, though a wide variety of designs exist.
There are still a number of unsolved key problems in classical mechanics and control theory, which are of crucial importance to modern industrial robot applications. These research challenges include planning and control of the nominal motion of a robot while it is interacting with:
ROBOTNOR researchers are targeting the following scientific and engineering results: