Fields of competence
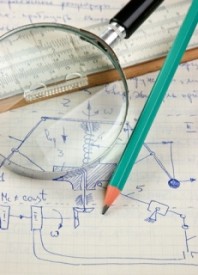
ROBOTNOR represents a unique synergy of academic and industrial expertise which allows us to counsel and comprehend a wide variety of tasks and projects. Our fields of competence are numerous and diverse.
Research project for robotic trimming of salmon fillets.
Practically all salmon fillets produced in Norway are trimmed clean of unwanted fat, bone remnants and other defects. In today’s modern salmon processing plants the trimming operation is performed by a combination of automated trimming machines and manual post-trimming. Manual post-trimming is necessary due to the inability of trimming machines to obtain satisfactory trimming for all fillets – in part due to trimming machines being limited to only a few specific trimming operations. Motivated by the observation that trimming of salmon fillets is still a labor-intensive processing operation, we set out to develop and demonstrate a prototype robotic system capable of being scaled up to adaptive and high-speed industrial robotic trimming of salmon fillets. The name of the prototype is RoboTrim and it is developed in a project financed by the Norwegian Research Council – “Novel sensor technology and automation for improved quality and process control”. The project as a whole is led by NOFIMA, and the RoboTrim subproject is led by SINTEF Fisheries and Aquaculture AS in cooperation with SINTEF ICT and SINTEF Raufoss Manufacturing AS. The project work was done at SINTEF Imaging and Automation Lab – a ROBOTNOR satellite laboratory located at SINTEF Fisheries and Aquaculture AS in Trondheim.
The design and methodology of RoboTrim focuses on developing an integrated system with the potential capability to perform any trimming operation that a human worker can. Our approach comprises 3D machine vision, a high-speed robot manipulator and a flexible light-weight cutting knife.
The developed prototype system was built and integrated – focusing so far only on a single trimming operation: the tail cut. Further research involves expanding and developing further the now integrated system so that it can handle also other cuts.
The different parts of RoboTrim were demonstrated in August 2013, and show that machine vision and robotices in the future may be employed in a more holistic and deeper level of automation of today’s processing lines. This next-generation deeper level of automation involves replacing manual labor for tasks such as detailed adaptive and non-uniform processing and handling that are still being done manually – despite the current use of shallow automation for uniform, bulk and high-level processing.